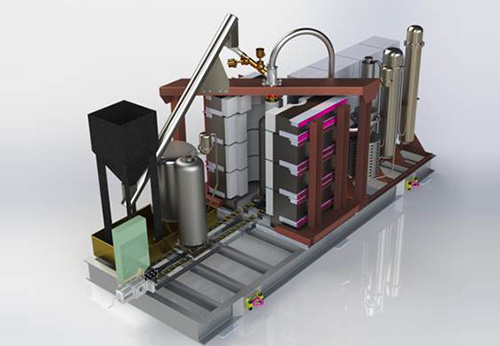
Dem & Melt: An innovative In-can vitrification process
In-can Vitrification Process for the conditioning of High and Intermediate Level Waste.
-
The nuclear industrial, research and D&D activities lead to a wide variety of medium to high level waste for which long-term management poses significant challenges. The great versatility of waste, in terms of shape and composition, poses difficulties to find an appropriate and economical management channel; some waste even does not have any routes.
The level of activity and lifetime of those waste often require a durable containment of the radionuclides as well as a chemical stabilization of the waste in order to meet the acceptance criteria for the long term disposal facility. In addition, the volume reduction is also a determining factor considering the technical and economic aspects of a geological disposal.
-
The DEM&MELT process is an innovative vitrification tool developed and designed to match the requirements and constraints of wastes streams from remediation or decommissioning and dismantling operations with no exit routes and for which handling, transportation and adapted conditioning matrix within the existing regulations have been identified as an issue.
The aim of this process is to provide a robust, simple and flexible in-can vitrification process to treat a diverse array of nuclear waste and materials ranging from intermediate to high level waste with different compositions and forms such as sludge, deposits, zeolites, liquids or solid wastes.
DEM&MELT is flexible to accommodate uncertainties in waste composition and is compact enough to be implemented in a decommissioned cell or close to the waste to be treated. The process allows a significant volume reduction in addition to safe radionuclides containment, and limited quantity of secondary waste. This in-can vitrification process has been also developed under a modular design in order to be adapted regarding to the nuclear operators needs minimizing investments and operating costs.
DEM&MELT design benefits from mature and proven technologies (from upstream functions to downstream functions) with over 40 years of Orano wide experience in high active operation at La Hague and Marcoule.
DEM&MELT is the result of a partnership between Orano, CEA, ECM Technologies and Andra.
It is supported by the French Government « Programme d’Investissement d’Avenir »[1].[1] « Programme d’investissement d’Avenir » is a French government investment program for higher education and research, initiated in 2010 and still ongoing in 2021
DEM&MELT offers several benefits for the operators such as:
- A simple, robust, flexible and competitive solution for treating intermediate and high level waste arising from remediation and D&D ;
- A solution compatible with and designed for a wide range of waste (liquids, zeolites, sludge, solids) ;
- Flexibility to accommodate uncertainties in waste composition ;
- A significant volume reduction, the safe containment of radionuclides and the stabilization of the waste ;
- A limited volume of secondary waste ;
- A compact solution allowing to be implemented in a decommissioned cell or close to the waste to be treated ;
- A modular design in order to be adapted regarding to nuclear operators needs minimizing investments and operating costs ;
- An integrated solution ranging from scenarios studies and matrix design definition to industrial operations.
-
A robuste, simple and versatile vitrification process:
- The container (or Can) is designed for a single use: it is used directly as a crucible. It has no stirring or pouring device. Corrosion issues are therefore limited ;
- The container is easily heated by a simple and robust resistance furnace, allowing efficient control of the temperature, cesium volatility management and homogeneity of the melted mixture ; Implementation, operation and maintenance costs are therefore lower than with furnaces using other heating technologies ;
- The process is relatively versatile and can handle highly active solid or liquid wastes with limited characterization. It can also operate at controlled temperature over a wide range ;
- Control of the process is simple and does not require advanced instrumentation ;
- An installation designed to generate a small amount of secondary waste ;
- Compact enough to be implemented in a decommissioned cell or close to the waste to be treated;
- Low investment and operation costs required.
A Modular design:
- Hands-on or remote operation and maintenance ;
- Batch process but continuous operation ;
- Ability to implement several furnaces in the same unit (fig.3) ;
- Dry or wet off gas treatment system depending on waste.
An integrated solution:
- Unique structure to provide a full and integrated solution, from matrix design to industrial implantation.
-