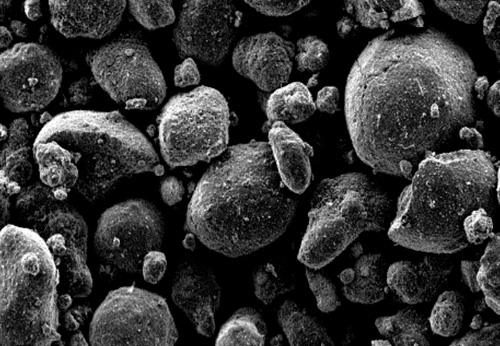
Precipitation : Fluidized bed precipitation
Process for preparing concentrates by fluidized bed precipitation.
-
In hydrometallurgy, processes usually end in a stage where the desired product is recovered in aqueous solution by precipitation, in order to convert the dissolved compound into a solid product.
Usually, precipitation is done by a traditional method in tanks, by batch or cascade. In this case, the final product can face issues related to fluidity, density, quantity of impurities, etc. These issues can lead to additional costs, especially concerning the transport of the final product.
-
To address these issues and reduce transportation costs for the final product, CIME can increase the apparent density of the final product by improving the precipitation process.
The solution is to precipitate in a fluidised bed reactor.
This method consists of preparing a uranium concentrate in the form of solid particles by precipitation from a uranium solution using a precipitation agent in a vertical reactor.
- Decrease in transportation costs
- Contribution to radiological safety
- Economic advantage when drying products
- Reduction of impurities and consequently, limitation of penalty costs
-
- Good filterability, which should not hinder production rates
- Fluidity of dry powder, an important characteristic during packaging.
- High density of the dry product, which allows the mass in the filled drums to be increased and thus considerable savings to be achieved on transport costs.
-
We have already licensed the cask in France and in Belgium for fissile content as B(U) package: Specifically developed for transport and storage of irradiated uranium residue equipped with special boron basket (fissile material)
The Innovation Center for Extractive Metallurgy or CIME from Orano Group develops scientific and technical solutions to meet the needs of its customers in the fields of energy, the environment, industrial recycling, health, minerals and ores processing and engineering.
The tripe function allows both to transport, store and dispose waste with the same cask.
-