Home
/
Catalog
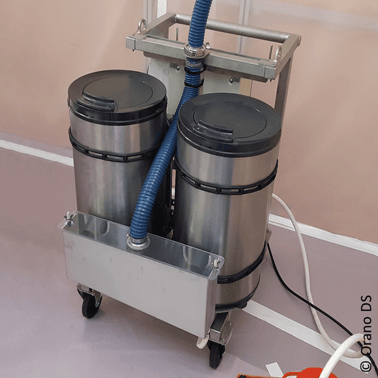
Twister : a process for drying wet textiles by centrifugation
An industrial processing tool for drying wet textiles by centrifugation.
-
During deconstruction operations, textile supports are used to absorb residual liquids or to decontaminate equipment with liquid reagents.
The management of wet textile waste in a nuclear environment is subject to stringent requirements to ensure that no free aqueous liquids are present during the waste handling process (transport, compaction, storage, incineration, disposal, etc.)
The compatibility of the treated waste with the producers' "dry waste" channels is ensured by :
- At a minimum, the absence of drips for simple manual pressing.
- Preferably, compacting the waste under an industrial press.
These operations are often time-consuming and labour-intensive, and incompatible with industrial processing rates. How can producers be given an alternative treatment solution to current practices ?
-
TWISTER is a mobile, compact and autonomous unit designed for ultra fast drying of wet textiles by high speed centrifugation (2800 rpm). The solution has been developed to satisfy the different configurations and needs of our customers :- Possibility of installing the spin dryers alone in a fixed station,- Operation of a single centrifuge for micro-bins- Possibility of long cycle treatments (reaching dryness levels above 90%),- Treatment compatible with a wide range of fibrous waste (e.g. glass wool, rock wool, etc.). The proposed unit is ergonomic and equipped with two spinners allowing the optimization of the treatment rates of an operator. This unit is simple to use and robust, without complex electronic or mechanical components. The exudation performances are high with a treatment time lower than 2 minutes for a batch of 10 to 15 liters. The solution has been qualified by numerous tests on the treatment of textiles soaked in aqueous liquids. The process for the treatment of textiles soaked with "oily/greasy" organic liquids is under development.Significant reduction in processing time compared to current practices (divided by >10 compared to a ventilated hood). Elimination of non-conformities by the absence of free liquid in the waste packages. Safe system allowing a secure use for the operator. Robust "zero maintenance" system. Very good exudation performance allowing compatibility with "dry waste".
-
Processing time less than 2 minutes per batch.Two parallel centrifugation units for continuous processing:Drying capacity: 300 l/hUp to 600 l/h at maximum performanceHigh exudation performance:Major reduction in processing time compared to current practices (divided by >10 compared to a ventilated hood). Up to 90% dryness for synthetic textiles, compatible with most producers' dry waste streams. Compact and easy to use mobile unit, without risk for the operator. Autonomous collection and lifting of effluents.
-