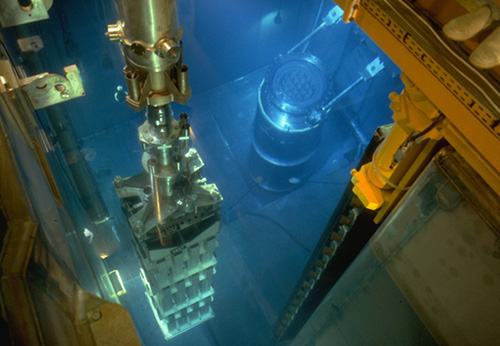
Used fuel reprocessing and recycling
Used fuel reprocessing and recycling saves natural resources and offers several benefits for operators, reducing risks and costs and allowing safe and long-term storage of waste conditioned in a universal canister.
-
In a context where operators and organizations in charge of used fuel management face several challenges such as saturation of the pools, delays of final disposal projects, necessity of multiple operations related to the management of interim storage (Issues with fuel integrity for extended dry storage period, ageing management with potential reconditioning required, repacking into final disposal canisters…)and are required by local or international authorities to define a used fuel management strategy up to disposal, used fuel reprocessing and recycling is a way to implement a safe, cost effective and sustainable strategy. This allows an optimized management of conditioned waste to be emplaced in future geological disposal facilities and the reuse of recyclable materials still contained in the used fuel, thus saving natural uranium resources and increasing the energetic independence.
-
Used fuel reprocessing and recycling is a mature technology implemented since decades by international nuclear operators leading to optimized waste conditioning.
Reprocessing is performed in the Orano La Hague facility with two steps:
- The reprocessing of the used fuel with the extraction of the recyclable materials (Uranium & Plutonium) from the used fuel, representing 96% of nuclear materials contained in used fuel;
- The conditioning of the non-recyclable materials considered as waste (fission products representing 4% of the nuclear material & non soluble metallic parts) in respectively vitrified and compacted Universal Canisters;
Recycling is performed in the Orano Melox facility with:
- The manufacturing of recycled fuel: MOX (Mixed Oxyde) fuel being manufactured by Orano with the Plutonium extracted and ERU (Enriched Reprocessed Uranium) fuel being manufactured by third parties with the Uranium extracted.
- Mixed oxide (MOX) fuel fabrication taking place in five main stages from pelleting to assembly manufacturing. Depending on customer needs, the MOX fuel of plutonium and depleted uranium can contain between 3% and 12% plutonium.
Focus on MOX fabrication by Orano:
The extracted uranium and plutonium can be recycled to make new fuel assemblies. The plutonium is combined with depleted uranium to make MOX, a mixture of plutonium and uranium oxides. In its most common form, approximately 10% of MOX is plutonium. It can be used in practically all reactors currently in operation in the world, whether they are pressurized water reactors or boiling water reactors. Since it was first used in a German reactor in 1972, MOX fuel has been used in 44 reactors worldwide.
Currently, Orano is the only company to produce MOX fuel assemblies at its Melox plant. Opened in 1995, the plant produces enough MOX fuel each year to supply 25 to 30 reactors as a supplement to enriched uranium fuels. Its production capacity has just been increased with the installation of a second powder mixing line, the first stage in MOX fabrication. This new equipment facilitates the production of mixtures meeting the specifications of various customers, providing additional guarantees of on-time delivery.
Secure & Rationalize deep geological repository by conditioning HL waste in a concentrated, stable and standardized form relieved from IAEA safeguards thus reducing the risks associated with long-term management of radioactive materials and leading to strongly optimized disposal facility.
High visibility and predictability of the costs avoiding the covering of future uncertain expenses inherent to open cycle used fuel management options (cost for initial interim storage, provision for extended storage and ageing management, potential reconditioning required etc…)
MOX fuel fabrication is an effective way to manage nuclear materials and which conserves uranium resources. In particular, it offers a way to deal with the issue of highly radioactive plutonium.
-
Orano reprocessing and recycling services of used fuel comprises the following steps:
- Used fuel shipment to Orano La Hague reprocessing plant;
- Used fuel reprocessing separating the recyclable materials (U& Pu) from the final waste;
- Conditioning of the final waste (fission products are concentrated and vitrified, non-soluble metallic parts are compacted) in Universal Canisters, stored on Orano’s site for cooling before being returned to the country of origin.
- Manufacturing of recycled fuel in association with fuel designer:
- MOX fuel made of Plutonium and depleted Uranium - manufactured at Orano Melox plant with the Plutonium being produced from the reprocessing operations and the depleted Uranium being supplied by Orano.
- ERU fuel made of Enriched Reprocessed Uranium - Reprocessed Uranium being produced from the reprocessing operations, enrichment and fuel manufacture being performed by the same suppliers as for Natural Uranium.
- Shipment of fresh fuel to the operator’s nuclear power plant.
-