Home
/
Catalog
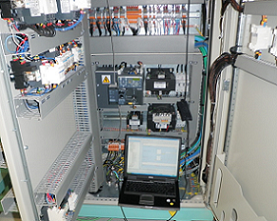
Commissioning industrial facilities
Validate requirements facility in terms of operation, safety and maintenance. Support the operating phase (training, operating procedures, diagnostic assistance, consulting).
-
Given the specific needs of high-risk industries, non-detection of malfunctions before commissioning may cause:
- Difficulties due to investigations and modifications (with significant cost-deadline consequences),
- A production capacity that does not comply with expectations,
- Possible consequences on safety demonstrations (credibility).
Hence, it is necessary to:
- Successfully and progressively commission facilities, making it possible to reach nominal performance levels as soon as possible,
- Optimise outages for maintenance throughout the operating phase.
-
To prepare for the test phase, Orano sets up upstream from this phase, a test engineer team suitable for the scope of the facilities. The identified steps are:
- Define from the design phases the test strategy to remove uncertainties and risks
- Develop validation plans and define prototypes or demonstrators
- Progressively integrate operating equipment and conditions
- Prepare, develop, analyse, and interpret the tests to demonstrate the operability and maintenance of facilities in nominal and degraded conditions
- Turn on equipment before transfer to ensure proper assembly
- Guarantee the safety of the tests and control over coactivity and safety
- Integrate configuration changes
- Make the evidence and demonstration of safety available
- Support the operator in the phases of training and preparation for operation.
- Removal of risks as soon as possible (remote tests)
- Complete tests guaranteeing normal and degraded operation
- Maintenance operations in non-accessible areas validated
- Exchanges with authorities simplified
- Faster rate increase
- Outage times optimised
- Training of operating personnel with optional assignment to tests teams
-
- Approach that integrates tests as soon as possible in project teams (strategy, validation plan)
- Performing tests that ensure the safety of people and property: test preparation, test progressivity, facility transfer
- Facility compliance with expected requirements
- Validating the maintainability of equipment particulary in inaccessible areas
- Providing support during commissioning
-
-