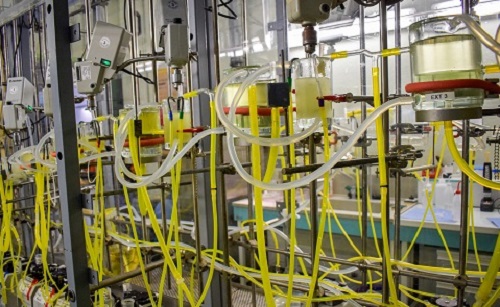
Process: Solvent extraction
An innovative and efficient process to extract co-products
-
Liquid-liquid extraction is a roll-separation technology in processes associated with nuclear recycling and mining. Unlike distillation technologies (separation based on boiling point differences), solvent-liquid extraction separates species of interest based on their differences in solubility between two non-miscible liquids.
In most cases of mineral reprocessing for the mining industry, solvent extraction is a preferred option to recover an element or to clean and purify a product. However, the complexity of mixtures resulting from mineral processing (acid nature, complex matrix, etc.) makes it difficult to develop, optimise and design solvent extraction processes.
-
In collaboration with internal and external plant operators, CIME has developed a strong expertise in solvent extraction using different technologies such as the mixer-stabiliser, the turbulent column and the pulsed column, to best meet the needs of its customers. In addition, the CIME infrastructure is designed to develop processes from the laboratory scale to the semi-industrial scale.
CIME is a key partner for manufacturers facing problems of recovery and/or restoration of by-products. CIME offers to use its infrastructure and expertise to develop, adapt and implement solutions for the treatment of leached minerals, the recovery of uranium and rare earths and the treatment of industrial waste.
CIME also provides solutions to chemical industry stakeholders on waste and effluent treatment, process optimisation and by-product recovery using solvent extraction.
Optimised by-product recovery using a high-efficiency element extraction process, selectively from a complex matrix deriving only a flow out of your production plant.
- The extraction phase is regenerated at the end of the extraction cycle.
- Allows the separation of components with (i) closed structures, (ii) closed boiling points and/or (iii) thermosensitive components.
- Great flexibility with regard to the physico-chemical properties of the mixture to obtain a final product of great purity.
- Efficient extraction of almost all elements of the periodic table.
- Limited environmental footprint.
-
- A modular and economical process designed to adapt to the specific nature(s) of the waste (origin, physical form, etc.) as well as to the challenges associated with it (treatment, recovery, disposal, etc.).
- Obtaining a final product of high purity even from a complex matrix and separating even very similar metals/elements with high yields.
- The ability to withstand very high flow rates and kinetically slow reactions
- A process that has already demonstrated its performance, particularly in the metal refining industry.
-
-
-