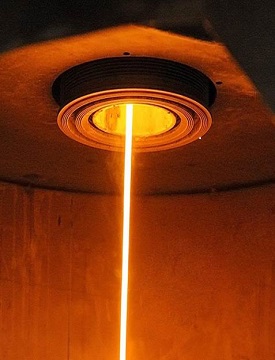
Vitrifying hazardous radioactive waste
Vitrification will bring you a definitive solution for controlling hazards from your wastes and ensuring long-term stability thanks to a safe and proven conditioning approach, the outcome of 40-years’ experience.
-
Succeed in managing your wastes which:
- need a wasteform which is safe and stable over time controling radioactivity impact on environment and humans,
- cannot be routed to standard surface disposal facilities,
- cannot be processed using traditional technologies such as grouting,
- need a wasteform versatile enough to integrate very different chemical elements.
-
Vitrification is a solution to process radioactive and hazardous wastes that cannot be processed using traditional technologies.
Alone or coupled with other treatment such as organic wastes incineration or melting of metals, it neutralizes the hazardous characteristic of the waste, destroys unwanted reactivity, and produces an inert, stable wasteform, suitable for safe long-term disposal, with attractive volume reduction ratios.
Our vitrification technologies are capable of simultaneously treating your organic, inorganic and metallic wastes, depending on the configuration chosen. A wide range of solutions have been or are currently being developed by Orano:
- In-can process (DEM&MELT),
- Incineration-vitrification in a cold crucible melter (vitrification of ashes coming from organic wastes incineration),
- Plasma-enhanced, incineration-vitrification process (PIVIC – organic wastes incineration before vitrification and metallic wastes fusion),
- Calcination and hot wall melter or cold-crucible melter.
- Definitive hazard elimination for a wide range of waste,
- Waste is transformed into an inert and durable wasteform, product ready for final disposal,
- Significant volume reduction (by a factor of up to 5 according to waste),
- Cost and delay optimization for waste treatment using the most adapted vitrification treatment (type of waste, type of hazard, activity level, layout constraints, site configuration…),
- Project support by a team of R&D, design and operation expertise.
-
- Waste is transformed into an inert and durable wasteform,
- Significant volume reduction,
- Product ready for final disposal,
- Operable, maintainable, and adaptable facilities, suited to any environment,
- Several technologies available according to waste type and context.
-
-