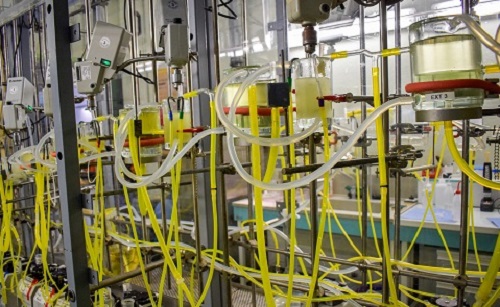
Procédé : Extraction par solvant
Un procédé innovant et performant pour extraire des co-produits
-
L'extraction liquide-liquide est une technologie de séparation par roulage dans les procédés associés au recyclage nucléaire et à l'exploitation minière. Contrairement aux technologies de distillation (séparation basée sur les différences de point d'ébullition), l'extraction liquide-liquide par solvant sépare les espèces d'intérêt en fonction de leurs différences de solubilité entre deux liquides non miscibles.
Dans la plupart des cas de retraitement des minéraux pour l'industrie minière, l'extraction par solvant est une option à privilégier pour récupérer un élément ou pour dépolluer et purifier un produit. Cependant, la complexité des mélanges résultant des traitements minéraux miniers (nature de l'acide, matrice complexe,...) rend difficile le développement, l'optimisation et la conception des procédés d'extraction par solvants.
-
En collaboration avec des opérateurs d'installations internes et externes, le CIME a développé une forte expertise dans l'extraction des solvants en utilisant différentes technologies telles que le mélangeur-stabilisateur, la colonne turbulente et la colonne pulsée, pour répondre au mieux aux besoins de ses clients. De plus, les infrastructures du CIME sont dimensionnées pour développer des procédés à l'échelle du laboratoire jusqu'à l'échelle semi-industrielle.
Le CIME se veut un partenaire clé pour les industriels confrontés à des problématiques de valorisation, et/ou restauration des sous-produits. Le CIME propose d'utiliser ses infrastructures et son savoir-faire pour développer, adapter et mettre en œuvre des solutions pour le traitement des minerais lessivés, la récupération de l'uranium et des terres rares et le traitement des déchets industriels.
Le CIME apporte également des solutions aux acteurs de l'industrie chimique sur le traitement des déchets et effluents, l'optimisation des procédés et la valorisation des sous-produits en utilisant l’extraction par solvant.
Valorisation optimisée des sous-produits à l'aide d'un procédé d'extraction d'éléments à haute efficacité, sélectivement à partir d'une matrice complexe en dérivant uniquement un flux sortant de votre usine de production.
- La phase d'extraction est régénérée à la fin du cycle d'extraction.
- Permet la séparation de composants avec (i) des structures fermées, (ii) des points d'ébullition fermés et/ou (iii) des composants thermosensibles.
- Grande flexibilité en ce qui concerne les propriétés physico-chimiques du mélange pour obtenir un produit final de grande pureté.
- Extraction efficace de presque tous les éléments du tableau périodique.
- Empreinte environnementale limitée.
-
- Un procédé modulaire et économique visant à s'adapter à la (aux) spécificité(s) des déchets (origine, forme physique...) ainsi qu'aux enjeux qui leur sont associés (traitement, valorisation, élimination, etc...).
- L’obtention d’un produit final de haute pureté même à partir d'une matrice complexe et de séparer même des métaux/éléments très similaires avec un rendement élevé.
- La possibilité de supporter des débits très élevés et des réactions cinétiquement lentes
- Un procédé qui a déjà démontré ses performances notamment dans l’industrie de l’affinage des métaux.
-
-
-